About Us
OUR MISSION
The Indiana Ready Mixed Concrete Association’s primary stated objective is to expand the use of ready mixed concrete in the State of Indiana. The IRMCA supports and promotes the use of high quality Portland cement concrete in pavements, parking lots, structures, and residential construction. The Association serves as a marketing and promotional organization for its members and provides necessary technical support and industry resources.
OUR VISION
The IRMCA is in the process of developing a 10-year strategic plan that fulfills the needs of its statewide membership. The IRMCA seeks to be an Association that not only serves its membership but also challenges it to grow.
Enhancing the beauty of our state
The IRMCA exists to promote the use of Ready Mixed Concrete to enhance the beauty of Indiana, to add durability and safety to our roads, to achieve lower life-cycle costs, and to decrease its environmental impact.
IRMCA STAFF
PRESIDENT
Paul Winkle
Ozinga Ready Mix, Inc.
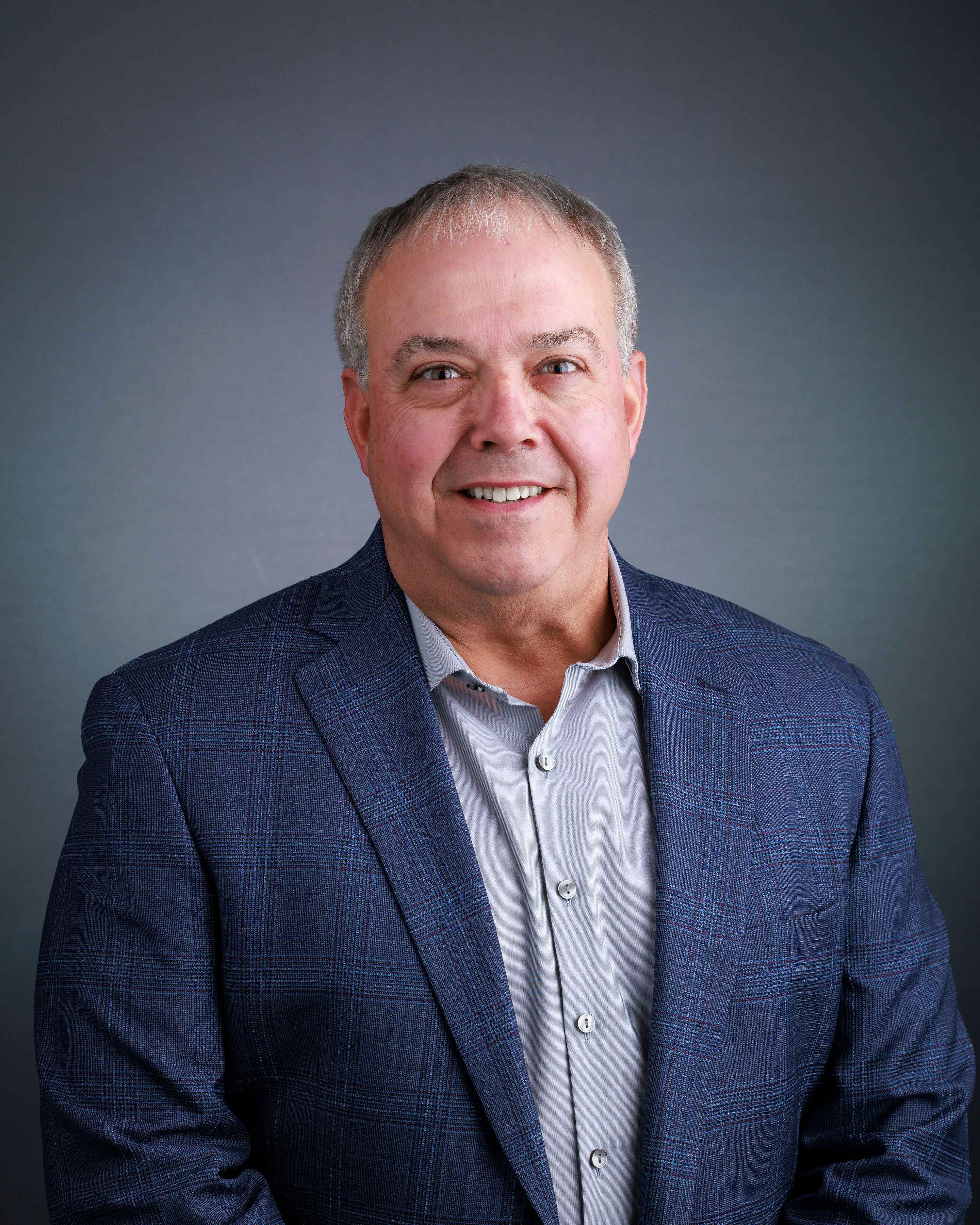
VICE PRESIDENT
Kevin Lemler
Irving Materials, Inc.
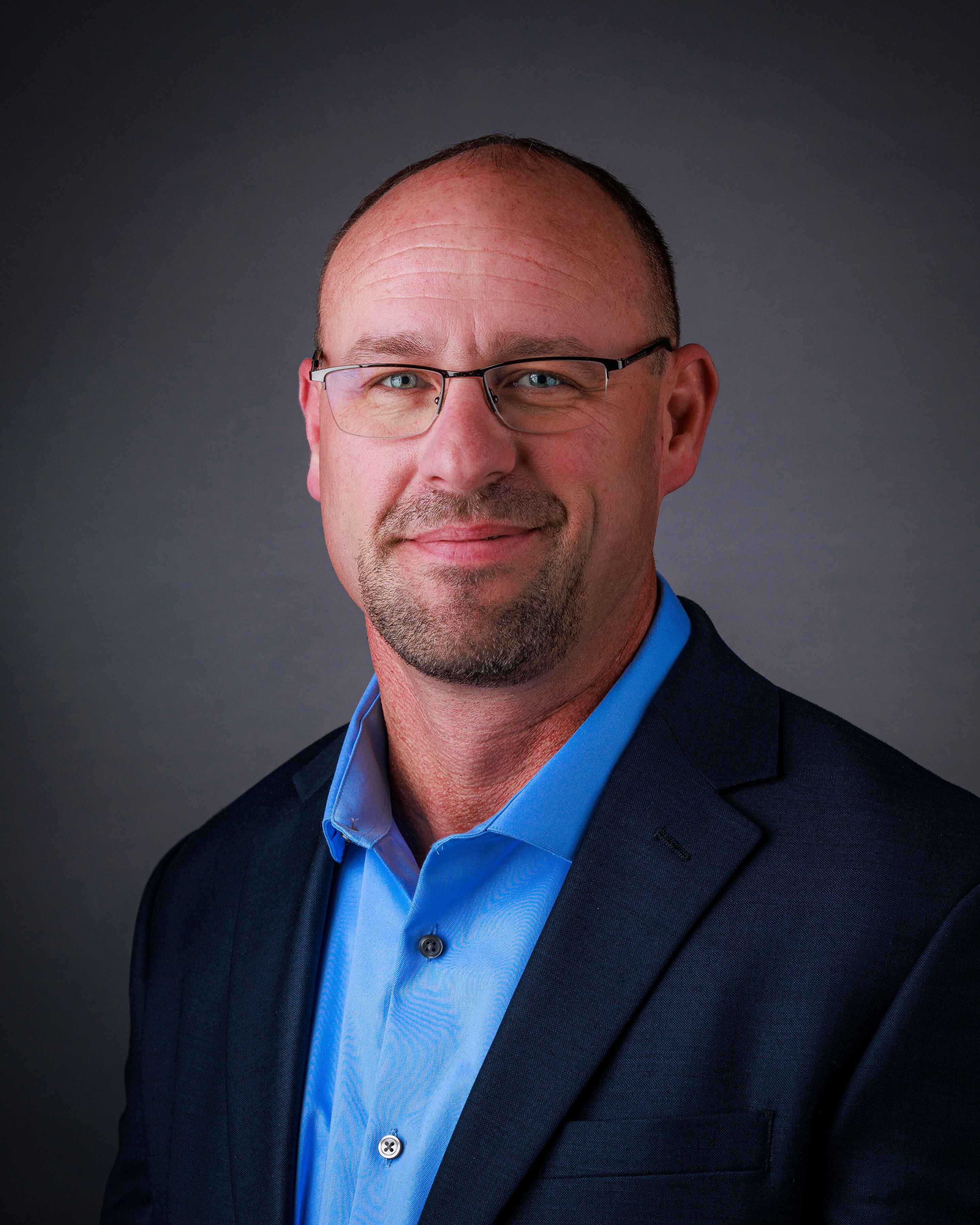
SECRETARY/TREASURER
Douglas Smith
Smith Ready Mix, Inc.
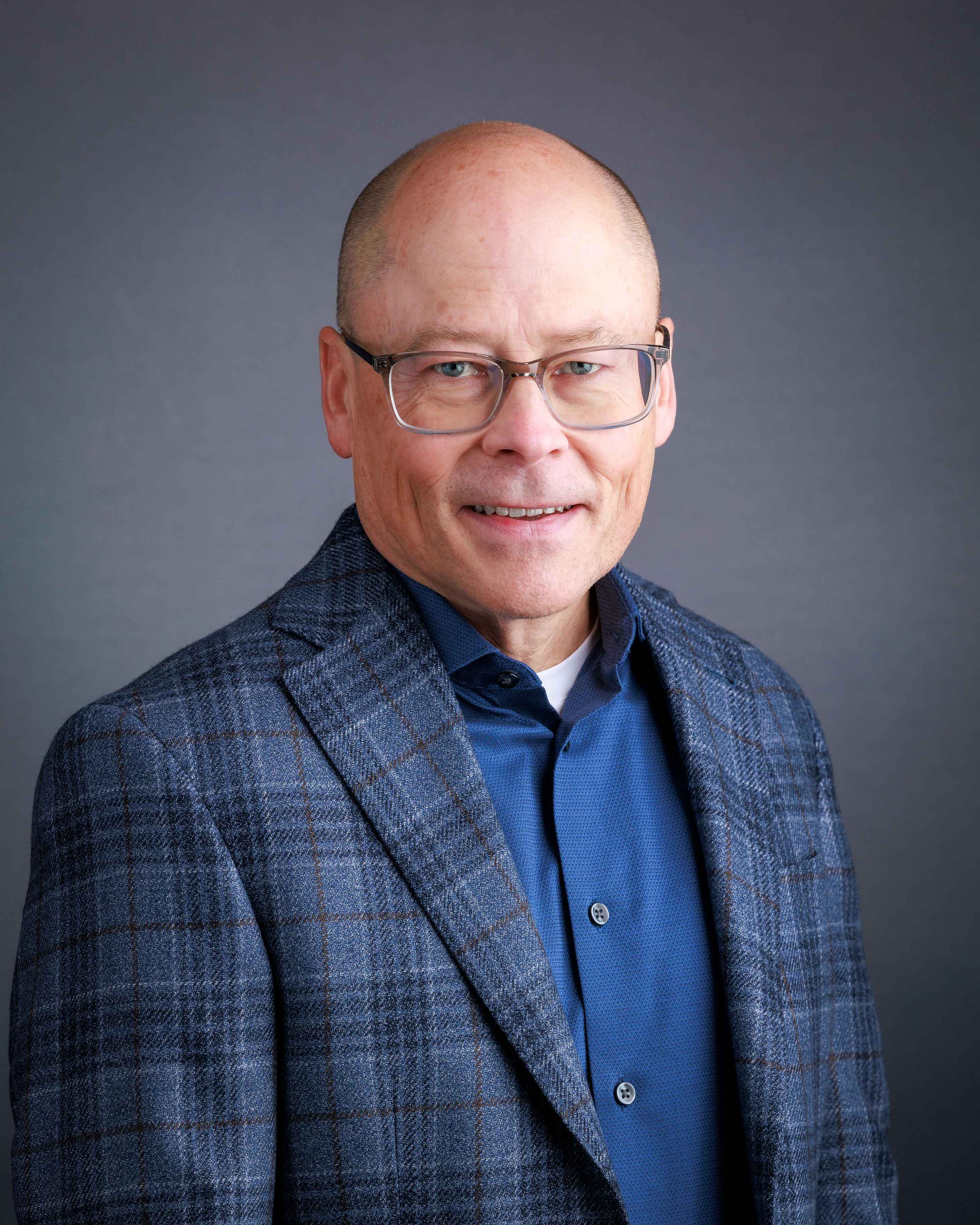
DIRECTOR
Clay McMillan
RussTech Admixtures, Inc
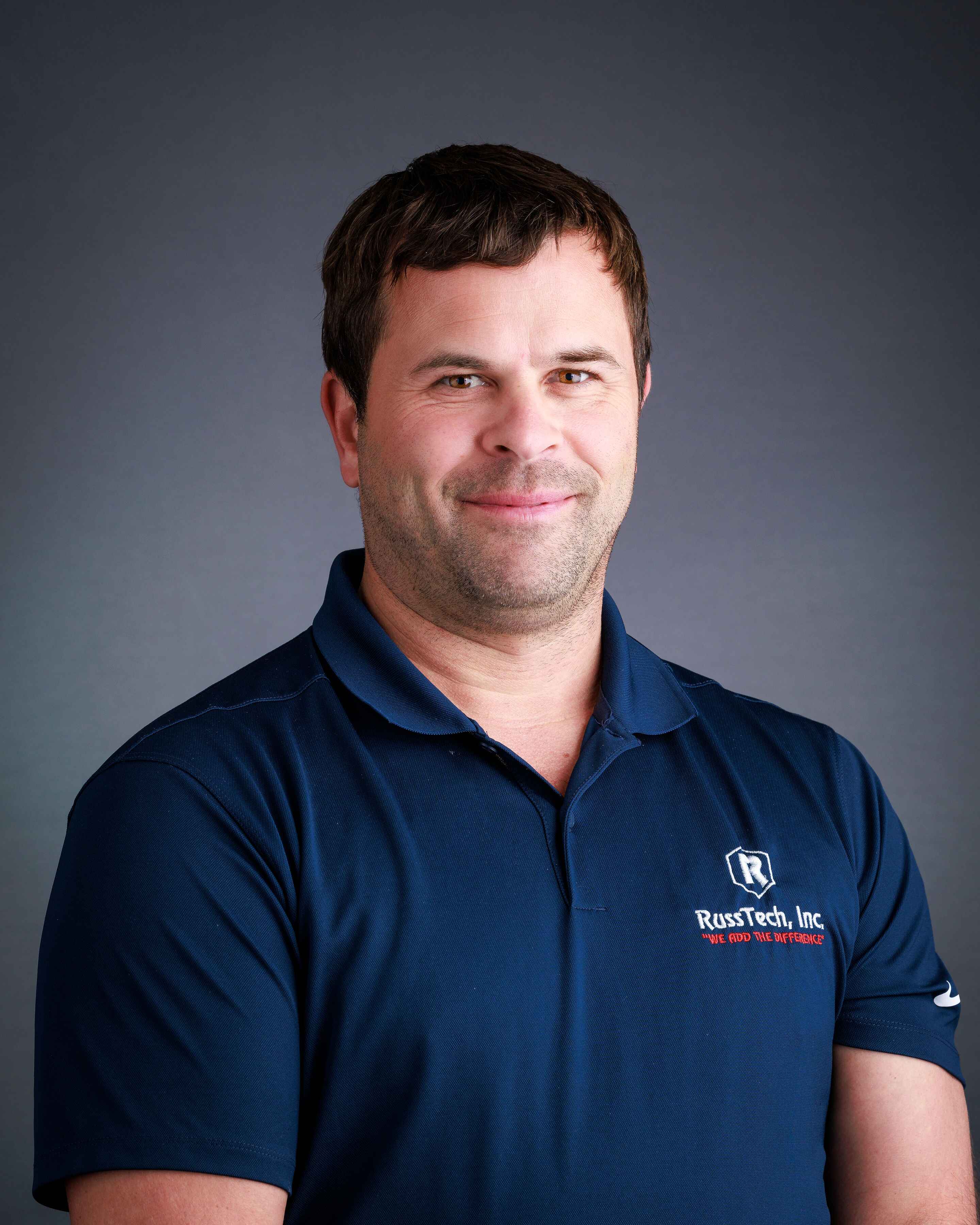
DIRECTOR
Matt Morrison
Kosmos Cement Company
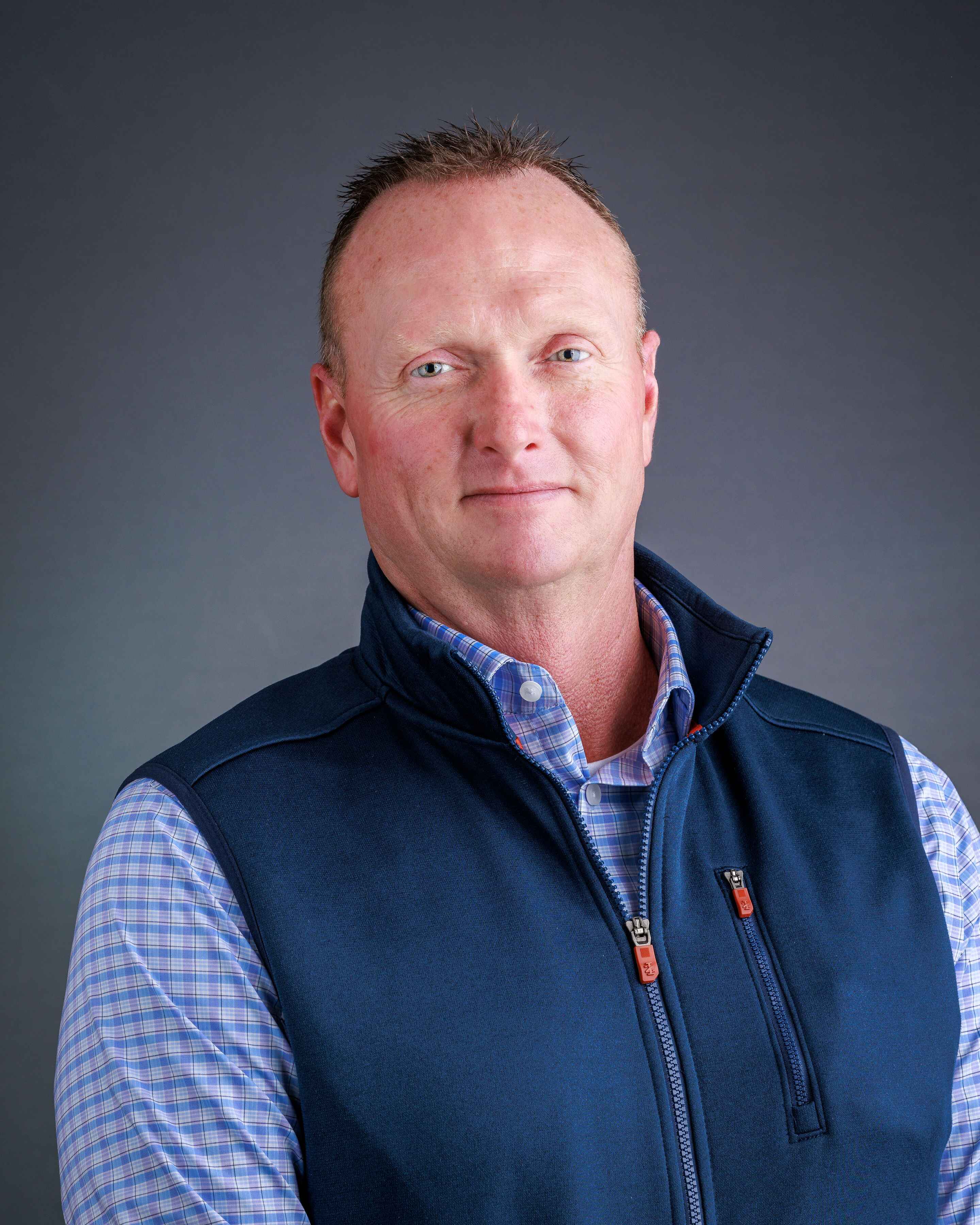
DIRECTOR
Rob Viola
Buzzi Unicem USA
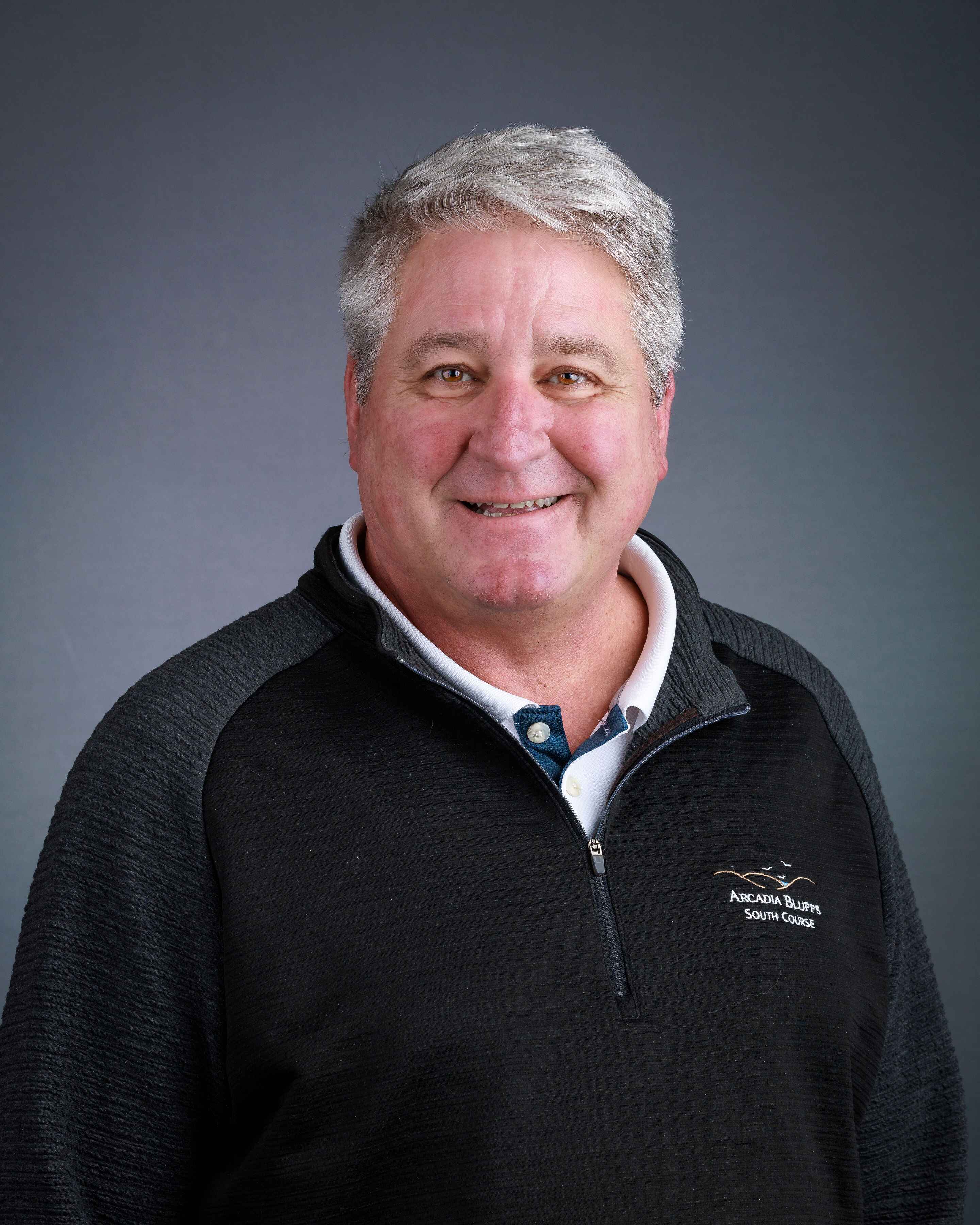
AT LARGE DIRECTOR, CENTRAL
Parker Haehl
Shelby Materials
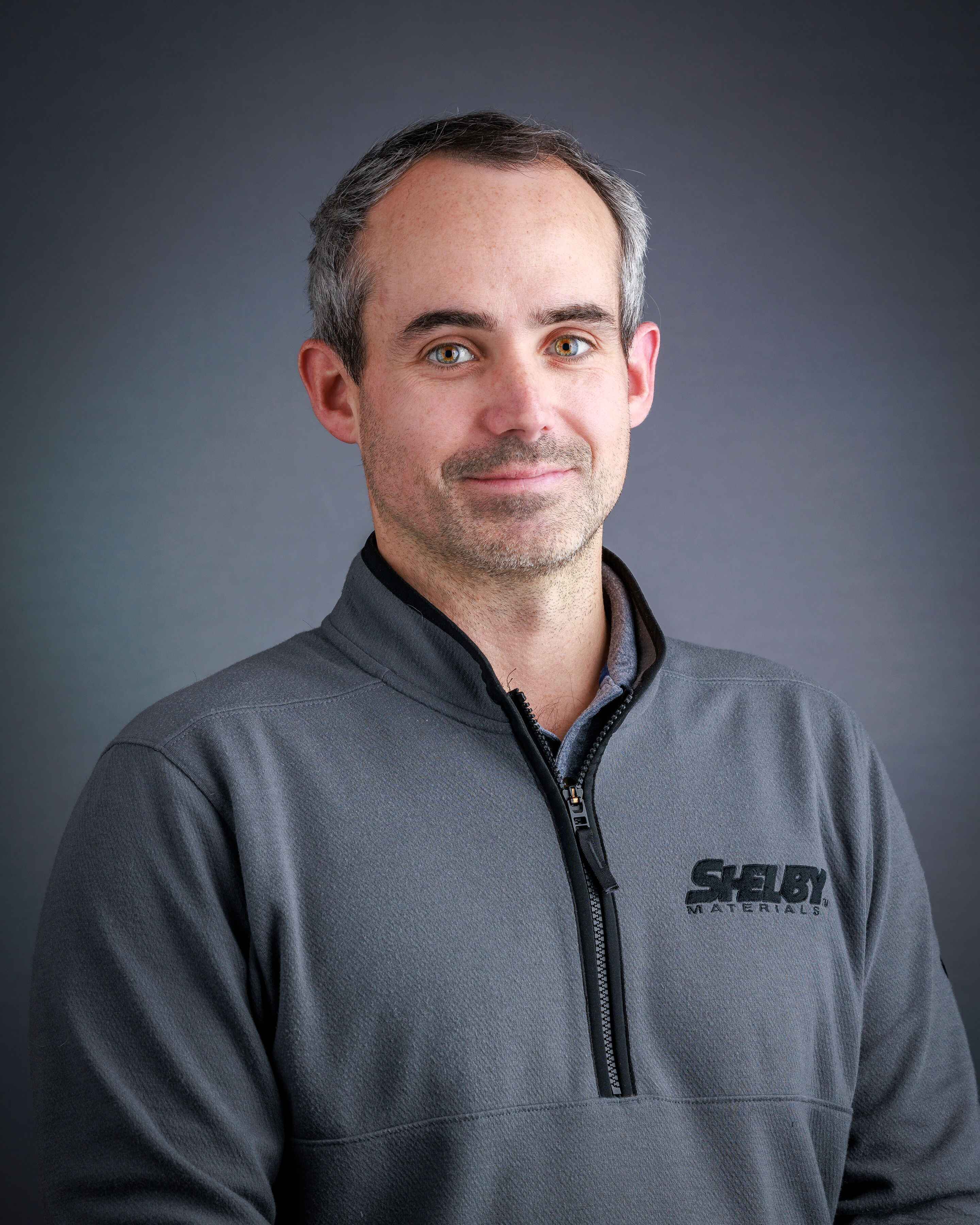
AT LARGE DIRECTOR, SOUTH
Jason Jones
Meuth Concrete
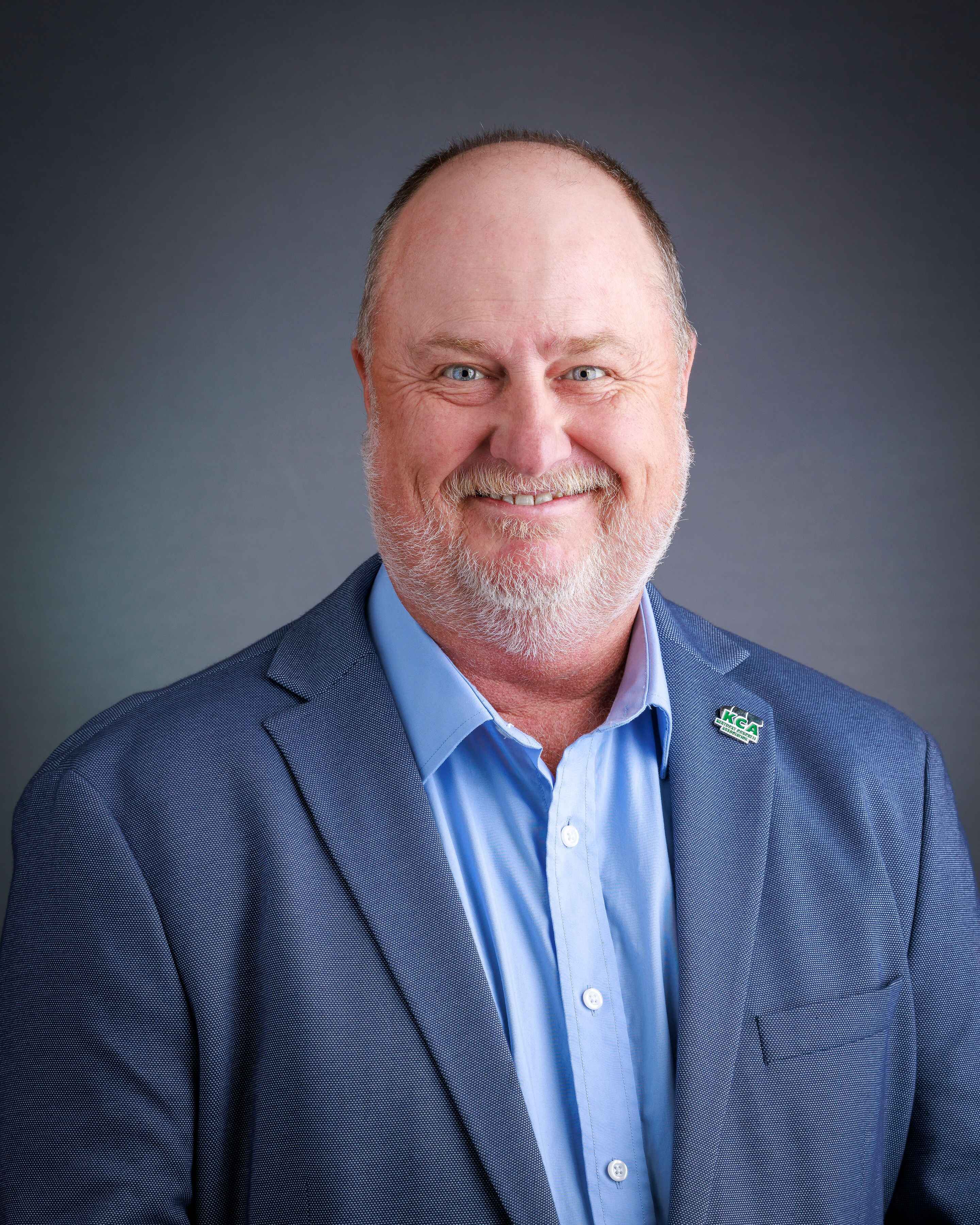
PAST PRESIDENT
Adam Kress
Ernst Concrete
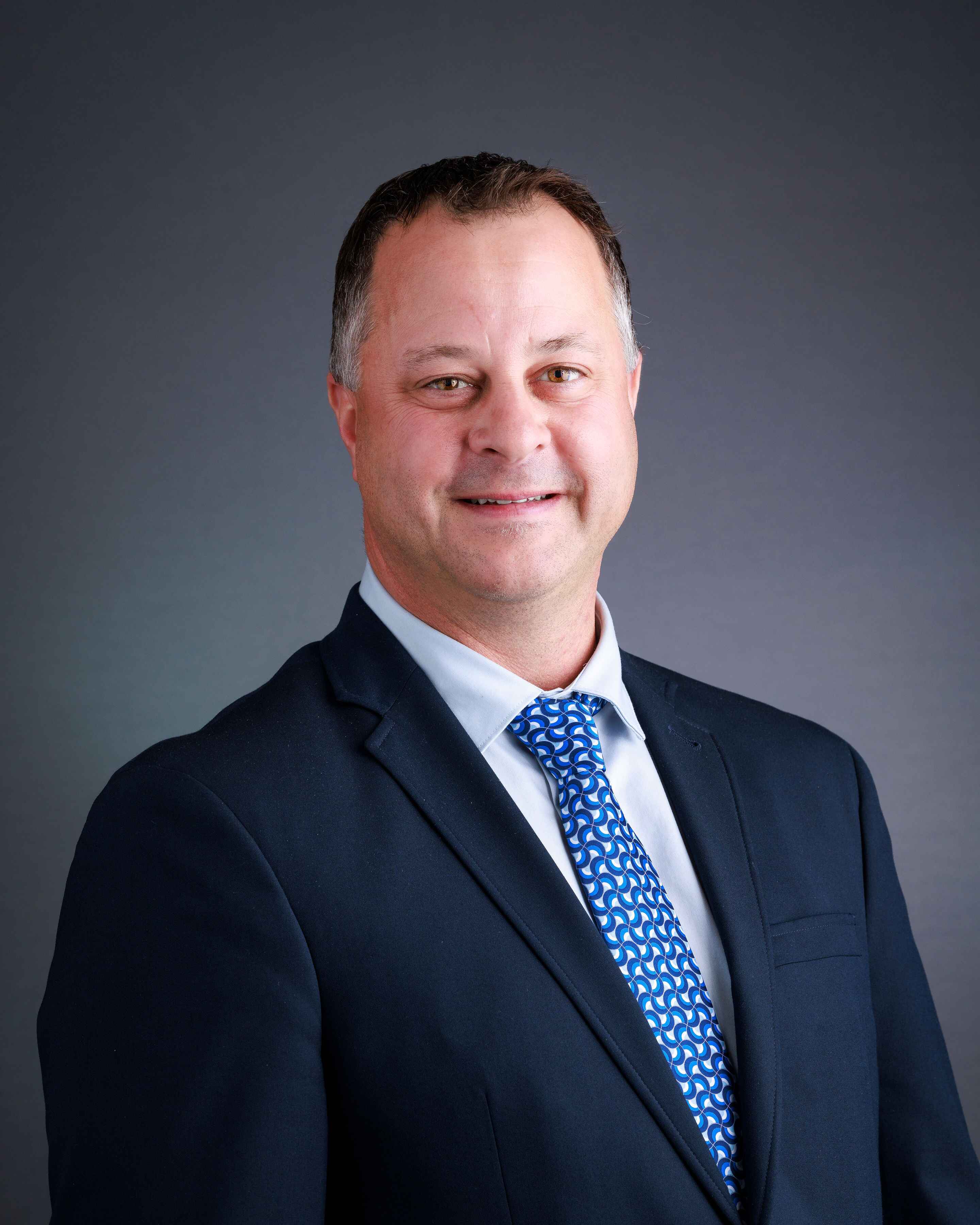
IRMCA Committees
Promotion Groups
The promotion groups meet on a regular basis, throughout different areas of the state, participating in educational breakfasts, pervious demonstrations, as well as planning and ACI testing.
Environmental and Safety Compliance Committee
This committee group addresses industry-related environmental and regulatory issues, as well as safety compliance information.
Tech-Ed Committees
The committee groups work to promote concrete usage, problem solve industry issues, and sponsor educational programs for members of the ready mix industry.
Concrete Professionals of Indiana [CPI]
The IRMCA-sponsored CPI group encourages newer, concrete professionals to network with fellow industry professionals and participate in philanthropy around the State of Indiana.
WHAT IS READY MIX CONCRETE?
Ideal for Many Jobs
Ready mixed concrete is particularly advantageous when small quantities of concrete or intermittent placing of concrete are required. Ready mixed concrete is also ideal for large jobs where space is limited and there is little room for a mixing plant and aggregate stockpiles. There are three principal categories of ready mixed concrete:
Transit mixed (also known as truck mixed) concrete, materials are batched at a central plant and are completely mixed in the truck in transit. Frequently, the concrete is partially mixed in transit and mixing is completed at the jobsite. Transit mixing keeps the water separate from the cement and aggregates and allows the concrete to be mixed immediately before placement at the construction site. This method avoids the problems of premature hardening and slump loss that result from potential delays in transportation or placement of central-mixed concrete. Additionally, transit mixing allows concrete to be hauled to construction sites further away from the plant. A disadvantage to transit mixed concrete, however, is that the truck capacity is smaller than that of the same truck containing central mixed concrete.
Ready mixed concrete is often remixed once it arrives at the jobsite to ensure that the proper slump is obtained. However, concrete that has been remixed tends to set more rapidly than concrete mixed only once. Materials, such as water and some varieties of admixtures, are often added to the concrete at the jobsite after it has been batched to ensure that the specified properties are attained before placement.
Shrink mixed concrete is used to increase the truck’s load capacity and retain the advantages of transit mixed concrete. In shrink mixed concrete, concrete is partially mixed at the plant to reduce or shrink the volume of the mixture and mixing is completed in transit or at the jobsite.
Proportioning
The key to strong and durable concrete is precise proportioning and thorough mixing of the ingredients.
Portland Cement and water form a paste that coats each particle of stone and sand, the aggregates. Through a chemical reaction called hydration, the cement paste hardens and gains strength over time.
If a mixture lacks paste, it cannot fill all the voids between aggregates. This concrete will be difficult to place and will produce rough surfaces and porous concrete.
Conversely, if a mixture has an excess amount of cement paste, it will be easy to place and will produce a smooth surface. However, the resulting concrete is not cost-effective and will crack more easily.
The quality of the paste determines the character of the concrete.
The strength of the paste depends on the ratio of water to cement. The water:cement ratio is the weight of the mixing water divided by the weight of the cement. High quality concrete is produced by lowering the water:cement ratio as much as possible, without sacrificing the ability to place, consolidate, and cure the fresh concrete.
A typical mix is about 10-15% cement, 60-75% aggregate, and 15-20% water. Entrained air in some concrete mixes may also occupy another 5-8% of the mixture.
Other Ingredients
Most drinkable water that has no pronounced taste or odor can be used as mixing water for concrete. Excessive impurities in mixing water can affect setting time and concrete strength, as well as; efflorescence, staining, corrosion of reinforcement, volume instability, and reduced durability. Concrete mixture specifications also set limits on chlorides, sulfates, alkalis, and solids found in the mixing water.
In contrast to mixing water, aggregates are chosen very carefully. Aggregates comprise 60-75% of the total volume of concrete. The type and size of aggregates used depend on the thickness and purpose of the final concrete product. Aggregates also need to be clean and free from any other matter that might affect the quality of the concrete. For efficient use of the paste, a continuous gradation of particle sizes is preferred.
Hydration Begins
After the aggregates, water, and Portland cement are combined, the mixture starts to quickly harden. This chemical reaction is called Hydration. All Portland cements are hydraulic cements that set and harden through this reaction. During this process, a node forms on the surface of each cement particle. The node grows and expands until it links up with nodes from other cement particles, or adheres to adjacent aggregates.
When the concrete is thoroughly mixed and workable it should be placed in forms before the mixture becomes too stiff. During placement, the concrete is consolidated in order to compact it within the forms and to eliminate potential flaws, such as honeycombs and air pockets.
For concrete slabs, the concrete is left to stand until the surface moisture film disappears, then a wood or metal hand float is used to smooth off the concrete. Floating produces a relatively even, but slightly rough, texture that has good slip resistance and is frequently used as a final finish for exterior slabs. If a smooth, hard, dense surface is required, floating is followed by steel troweling.
Curing
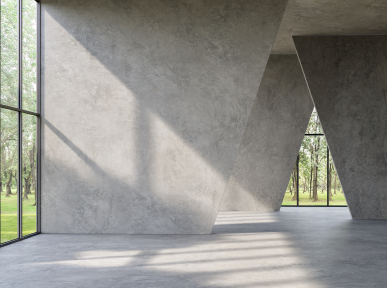
Curing begins after the exposed surfaces of the concrete have hardened sufficiently to resist marring. Through the process of curing, it ensures the continued hydration of the cement; so the concrete continues to gain strength. Concrete surfaces are cured by sprinkling with water fog, or by using moisture-retaining fabrics such as burlap or cotton mats. Other curing methods prevent evaporation of the water by sealing the surface with plastic or by using special sprays called Curing Compounds.
Special techniques are used for curing concrete during extremely cold or hot weather. The longer the concrete is kept moist, the stronger and more durable it will become. The rate of hardening depends on the composition and fineness of the cement, the mix proportions, and the moisture and temperature conditions.
Concrete continues to strengthen as it gets older. Most of the hydration and strength gain take place in the first month of concrete’s life cycle, but hydration still continues at a slower rate for many years following.